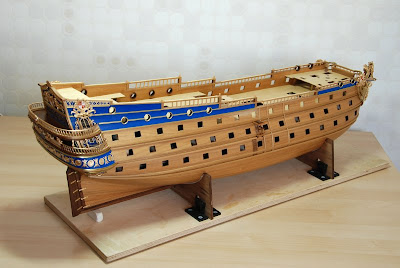
A couple of overall photo's of how the hull looks at this stage.
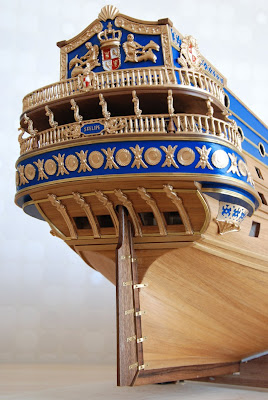
The stern almost complete just some canons and gun port lids to add.
The rudder in position, I was thouroughly pleased with how this turned out and it works just as good as it looked !
The hinge nearly finished, the sides had to be cut for length and the sides drilled ready for the pins o hold it in position.
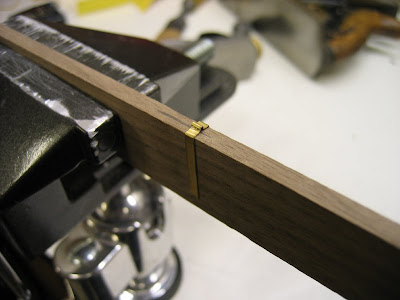.jpg)
The sides were then bent over a piece of timber the same thickness that was on the stern/rudder of the boat.
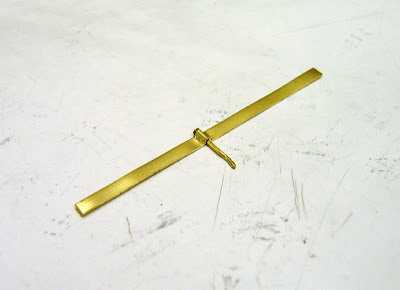.jpg)
It was then opened up and flattened on the bench with the pin still in position to make sure the hole did not close up.
It was then bent over a brass pin held in a vice.
I decided it was time to start the rudder on the stern, I also thought I would make my own hinges to suit exactly what I needed, I started with a piece of brass strip 3mm x 0.3mm, this was planed with a block plane to a with of 2.5mm.
The royal entrance door finished along with its canopy,steps and handrail.
The hole for the royal entrance doors was achieved by using the same technique as the gun ports, when I glued the royal entrance door into position I put a piece of masking tape through one gun port and out of another, this was to stop the door being pushed to far and
being lost forever in the bottom of the hull !